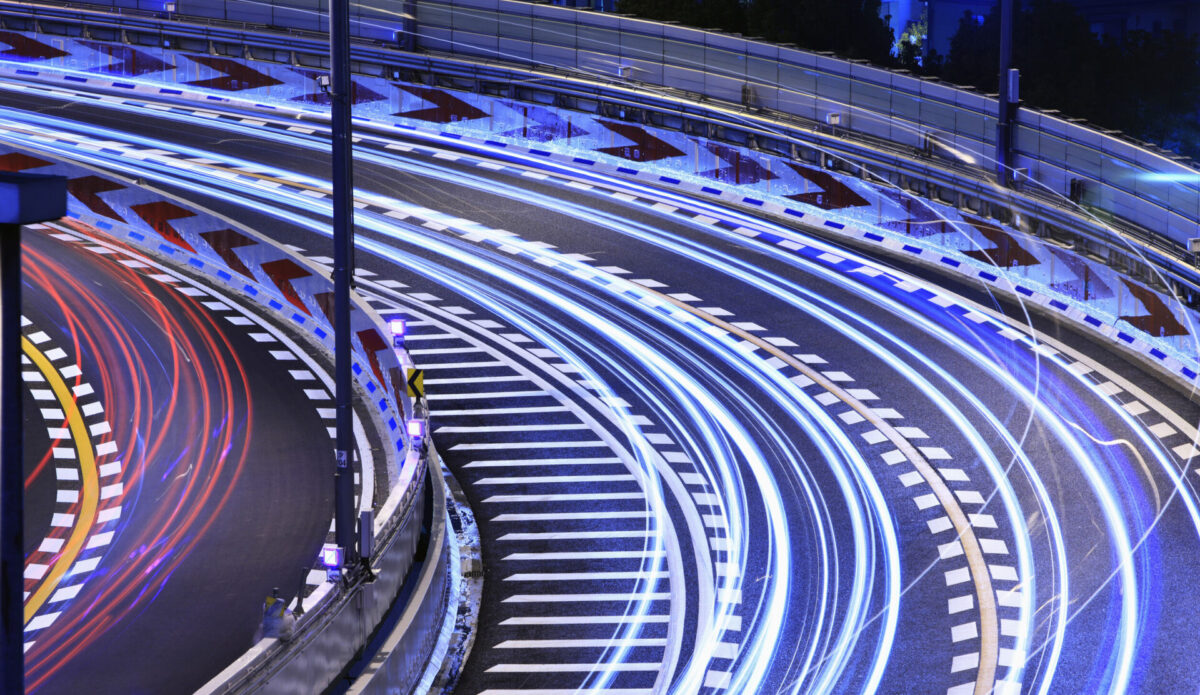
2022.06.30
執筆:物流・ITライター 坂田 良平
「もはや運送会社に配車を委ねるような余裕はないんですよ」──前編では、荷主が自ら配車を行おうとする理由について考えた。
だが、荷主が配車を行うのは簡単ではない。
理由は二つある。
一つは、たいていの荷主には配車を行うことができる人材がおらず、配車のノウハウがないから。
もう一つは、荷主が配車を行う場合、運送会社の配車と比べ、より多様な選択肢、条件、そして目的を満たさなければならないからだ。
後編となる本稿では、一般論として市井のパッケージ配車システムの課題と、荷主向けの配車システムに必要な要件を考えつつ、本テーマにおける構造計画研究所のアドバンテージを検証していきたい。
オールマイティな配車システムは存在しない
配車の三要素は、ルート、積み付け、コンプライアンスである。
世の配車担当者たちは、この三要素を勘案しつつ、最適な配車計画を立案しようと日々奮闘している。
コンプライアンスについて補足しておこう。ここで言うコンプライアンスとは、改善基準告示を筆頭とする労働基準をクリアし、トラックドライバーの働き方がコンプライアンスをクリアできることを指す。また、貨物(例えば毒物・劇物や大型・重量物など)によっては、道路通行許可等もクリアした配車計画を立案する必要がある。
パッケージ型の配車システムは、この配車の三要素について、それぞれ独自の味付けを行っている。
例えば、コンビニ配送などのミルクランを行う運送会社の場合、まず大切なのはコンプライアンスに則ったドライバーのシフト計画を立案することであり、その次に積み付けが続く。ルートに関しては固定されている場合が多いため、配車を行うたびに勘案する必要は少ない。
このようなミルクランを想定した配車システムでは、コンプライアンス、積み付け、ルートの順番で算出が行われる。
混載を主業とする場合、積み付けとルート最適化がそれぞれ重要となる。逆にコンプライアンスについては、改善基準告示の連続運転基準をクリアすれば、勤務間インターバルや休日については、重要視されないこともある。そもそも、標準勤務時間と休日をきちんと定めているケースも多いからである。
他にも、パッケージ配車システムの場合、ルート最適化に大きく比重をおいていて、積み付けについては貨物の総重量とトラックの積載量を比較し、過積載アラートを発報する程度の機能しか持たないものもある。
配車の三要素に対する比重の偏り──すなわち、配車システム会社側のこだわりがあるからこそ、配車システムの特色が出るし、特色があるからこそユーザー(運送会社や荷主)側は、自身の望む配車システムを選択しやすくなる。
逆に言えば、オールマイティな配車システムなど存在しない。
問題なのは、市井のパッケージ配車システムでは、自社のニーズを満たすことができない運送会社や荷主である。
まとめよう。
荷主が配車計画を自ら立案したいと考えるのであれば、まずは荷主自らが配車計画における基本ルールを定めなければならない(プロセス1.)。基本ルールでは、利用するリソース(倉庫や輸送手段の範囲)や、優先すべきルール(利益率や配送のリードタイムなど)を定める必要がある。定めた基本ルールを実現・実行できる配車システムを選定するのが、プロセス2.である。
「一番儲かる配車を算出して欲しい」
メーカー物流子会社C社のエピソードである。
それまでC社では、キーマンとなる配車担当者が一人で配車業務を行っていた。だがある日、配車担当者は緊急入院した。大動脈解離を発症したのだ。
C社の配送業務は、時間指定のある配送先が多く、また貨物量が多いため、2台以上のトラックで同じ配送先への配送を行うケースもあった。一人のドライバーが、午前中は2tトラック、午後は大型トラックというように、トラックを乗り換えて配送を行うことも、C社における配車業務の特殊性であった。
配車担当者の急病により、配車業務は大混乱した。特殊性が高い配車業務をこなせる人材が他にいなかったためである。配車担当者が業務復帰するまでの約1ヶ月、一部の仕事は断らざるを得ず、売上も落としてしまった。
この状態を業務遂行上のリスクと考えた営業所長は、配車システムの導入を模索し始めた。そこで、複数の配車システム会社と打ち合わせを開始した。
ところがである。
ある配車システム会社との打ち合わせで、役員がこんなことを言い始めたのだ。
「一番儲かる配車計画を立案できませんか?協力会社や、路線便、もっと言えば鉄道の利用も視野に入れて、もっとも利益の上がる配車計画を立案できる配車システムが欲しいんですよ」
実はC社では、1年ほど前からキャッシュアウトを減らすべく、協力会社の使用を制限していた。役員の発言は、自社車両での配送にこだわりすぎたため、かえって損益が悪化していた現状を憂いたものだ。
カスタマイズを模索したものの…
C社の希望を受け、ある配車システム会社(以下、配車システムD社とする)がカスタマイズの検討をしてくれることになった。打ち合わせは3ヶ月続いたが、ある日突然終了した。
「ごめんなさい、ギブアップです」、配車システムD社の技術担当者から連絡が入ったのだ。
配車システムD社がギブアップした最大の要因は、トラックの乗り換えであった。
どんな配車システムも、最適な配車計画を算出するためのエンジンを搭載している。技術担当者いわく、配車システムD社が提供する配車システムのエンジンでは、トラックの乗り換えに対応した配車計画を立案することができなかったのだ。
「エンジンが備えるアルゴリズムの肝の部分でもありますので、変更することができません」
技術担当者が、自社システムの肝となるエンジンのロジックを理解していなかったのだ。根本的に駄目である。
結局、C社は3ヶ月を棒に振ったことになる。
荷主に必要なのは、より幅広い選択肢から最適な配車計画を導くこと
C社は、倉庫の新設も含めてシミュレーションすることを希望していた。
当時、C社の物流センターは、都内一箇所のみであった。親会社の工場がある神奈川県西部から東京まで貨物を横持ちしてから、神奈川県内に対して配送を行っていたのだ。
試算したところ、神奈川県西部に新たな倉庫を借りても採算は取れるはずだった。だが、実際の配車計画にまで落とし込んでシミュレーションをしなければ、本当のところは分からない。
「パッケージ配車システムをカスタマイズして、C社希望の配車をできるようにしないとシミュレーションはできません」と、配車システムD社は説明していた。「まあ、そういうものかもしれない」と、C社も、そしてアドバイザーとして加わっていた筆者も考えてしまった。
今考えれば、これではC社にとって最適な配車システムを選択することは難しい。
荷主が、配車を自ら担うためには、二つのプロセスを経る必要がある。
- 最適化な配車基準を模索するプロセス。
- 標準化された配車標準に従い、実行できる配車システムを選定するプロセス。
1.のプロセスでは、物流センターの再配置なども含め、サプライチェーンの見直しも視野に入れて検証したいと考える荷主もいるだろう。検証のためには、シミュレーションを行うことも必要となる、
しかし、日々配車計画を立案する上では、ある程度絞った条件下で配車計画の算出(≒配車システムの運用)を行わなければ、手間がかかるだけである。極論だが、日々の実務の中で、物流センターの再配置を検証する必要はない。
まとめよう。
荷主が配車計画を自ら立案したいと考えるのであれば、まずは荷主自らが配車計画における基本ルールを定めなければならない(プロセス1.)。基本ルールでは、利用するリソース(倉庫や輸送手段の範囲)や、優先すべきルール(利益率や配送のリードタイムなど)を定める必要がある。定めた基本ルールを実現・実行できる配車システムを選定するのが、プロセス2.である。
「セミパッケージ+カスタマイズ」の可能性
ここからは、構造計画研究所の話をしよう。
構造計画研究所の強みは、「セミパッケージ+カスタマイズ」のソリューションを提供していることにある。
「セミパッケージ+カスタマイズ」──いわば、ソリューションのカスタムオーダーとも言うべきか。
配車計画の算出を担うエンジンの部分はパッケージ化されているが、そのエンジンのチューニングは、お客さまのニーズに応じ臨機応変にカスタマイズできる。これが構造計画研究所の強みとなる、「セミパッケージ+カスタマイズ」の言わんとするところである。
システムの肝となるエンジンだが、必ずしもシステム会社が自社で設計・制作しているとは限らない。私がかつて取り扱っていた配車システムのエンジンはGoogleのAPIを利用していたし、他の配車システム会社でも、エンジンの部分は外注しているケースがある。
対して、構造計画研究所では、自社でエンジンを作り上げている。
だから、お客さまから「○○という条件で、配車シミュレーションを行って欲しい」と依頼があれば、エンジンに直接データを放り込んで(もちろん比喩的な表現である)、「はいどうぞ!」とシミュレーション結果を提供することも比較的容易なのだ。
さらに言えば、エンジンのアルゴリズムやパラメーターをチューニングすることによって、市井のパッケージ配車システムでは実現不可能な配車計画ロジックをシステム化することも可能だ。
以下は一般論である。
パッケージソリューションで望む結果を得られるのであれば、迷わずパッケージソリューションを選ぶべきである。安定した性能を比較的手頃な価格で利用できるメリットは大きい。
パッケージソリューションをカスタマイズするという手もある。
だがこの場合、カスタマイズできる範囲には限度があり、結果としてあなたの望む機能を十分に満たせない可能性も考慮しておくべきだ。
フルスクラッチで、新たにソリューションを構築するという手もある。
だがこの場合、ソリューション構築費用は(特にパッケージソリューションに比べ)はるかに高額になるし、また構築までに時間が掛かることも覚悟すべきだ。
構造計画研究所が提供する「セミパッケージ+カスタマイズ」は、これらのメリットとデメリットをバランスよく、しかも最適に解決する方策として、注目に値する。
真に最適な配車を生み出せるのは、サプライチェーンの担い手たる荷主
国土交通省、経済産業省は、フィジカルインターネット実現会議において「物流危機」という強い言葉で、今の物流のあり方について懸念を表明した。
物流危機の文脈を鑑みれば、「自ら配車を行いたい(行うべきだ)」と考える荷主が登場するのは当然だろう。
物流の最適化とは言うものの、物流だけを最適化しても本質的な改善にはつながらない。
物流とはサプライチェーンの一部分でしかなく、したがって真に最適な物流を生み出すためには、サプライチェーンの最適化を目指さなければならない。
そしてサプライチェーンの最適化の主役は、物流企業ではなく、メーカー、小売、卸などの荷主である。言ってみれば、真の物流最適化を実現できるのは、倉庫会社、運送会社といった物流企業ではなく、荷主なのだ。
だがこれまでは、「自ら配車を行いたい(行うべきだ)」と考えても、その実現をサポートする適切な配車ソリューションが存在しなかったと筆者は考えている。あくまで筆者の私見ではあるが、構造計画研究所の取り組みに、「ようやく真打ち登場か!?」と期待している。
荷主が適切な配車を自ら行うことができれば、きっと良い結果を生む。
一例として積載率を考えよう。
1993年に5割以上だった営業用トラックの積載率は、現在では4割以下まで低下している。荷主自ら配車を行うことで、積載率を向上させられる可能性は高い。
荷主が帰り荷も含めて貨物を手配できれば運送会社もハッピーだし、荷主自身も配送効率を高め、ひいては貨物あたりの物流単価低下というメリットを得る。
本稿を読み、「それはうちのことだ…!?」と感じた人がいるのであれば。
ぜひ、構造計画研究所にアプローチして欲しい。