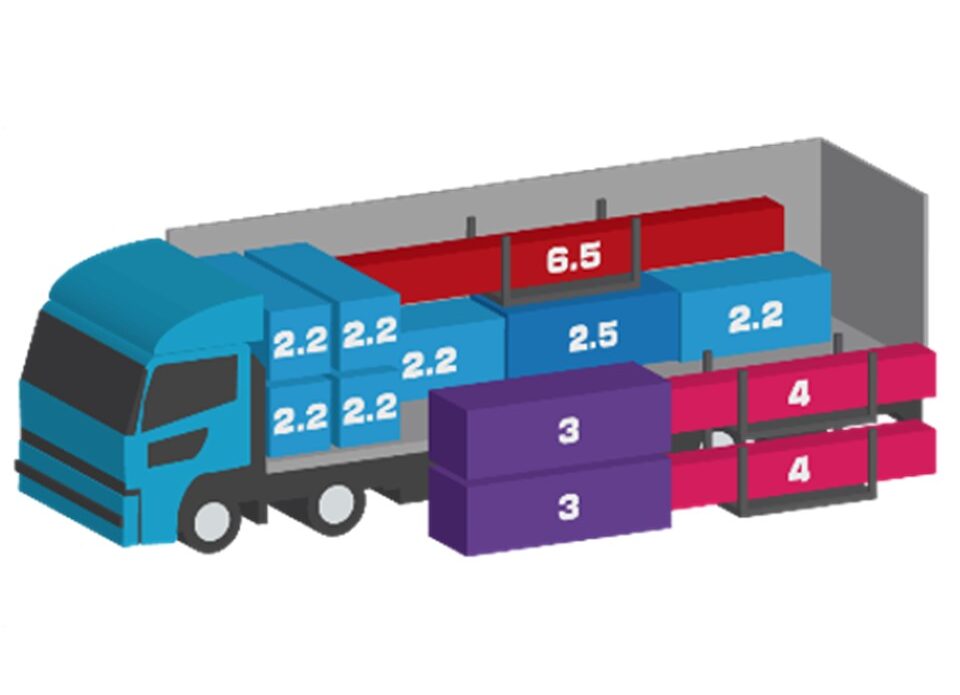
2022.06.30
「形状・サイズが多様な製品をパレット化して輸送。そこで生じたトラック積載率の大幅低下を、『積み付けプロジェクト』で解消しました」
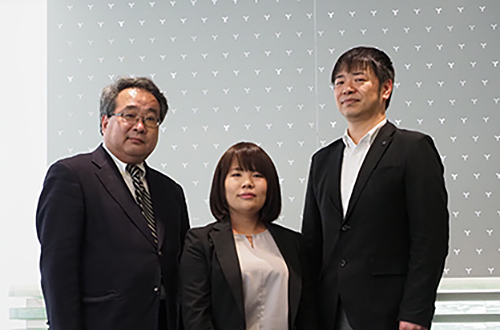
物流業界では運転手不足を背景に、荷主にとって輸送コスト上昇への対応、安定的なトラックの確保などが急務になっている。大手建材メーカーYKK APは、構造計画研究所(KKE)の提案に基づきトラックへの効率的な「積み付け」を実現、運賃単価の大幅な削減とともに、物流業者の負担軽減に成果を上げた。同社生産本部ロジスティクス部 業務情報開発室長の四柳博之氏、技術・開発担当の最上光雄氏、同業務情報開発室田中愛子氏に、プロジェクトの意義、今後の展望についてうかがった。
「バラ積みで満載」が許されない時代になった
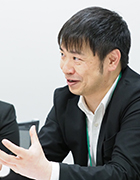
生産本部 ロジスティクス部
四柳 氏
ー ロジスティクスの改善を迫られたのには、御社ならではの事情もありました
我々が生産する窓やサッシ部材は、形やサイズがまちまちで、板状の製品もあれば、長さが6mを超えるような長尺のものもあります。従来は、これらをトラックにバラ積みしていました。隙間なく積めば、効率よく運ぶことはできます。でも、積み下ろしをするのは人間。具体的には輸送を委託した業者に、全てお任せしていました。10tトラックの場合、積むのも下ろすのも3時間はかかる。人手不足の中、そういう「わがままな荷主」は、敬遠されかねない状況でした。お客さまだけでなく、関わる全ての人たちに「善の巡環」を、という当社の精神にも反します。
そこで、2015年からパレット輸送を始めたのですが、今度は運賃単価の上昇という問題を招いてしまいました。積み荷をパレット化すると、確かに積み下ろしは楽で、ドライバーは運転に専念できます。しかし、先述したように多様な製品をパレットに載せて運ぼうとすると、荷台に多くの隙間が生じ、積載率が低下してしまうのです。実際には、積載可能容積が40%もダウンし、当然、そのぶん多くのトラックを頼まなくてはならない=物流コストのアップが避けられない、という事態に陥ったわけです。
ー ご相談いただき、「積み付けプロジェクト」をスタートさせたのが、2015年7月です
積み付けに関するソフトを持つ会社は多々ありましたが、当社のような「特殊な荷物」に対するソリューションを提供してもらえるのは、KKEだけでした。他社は、「ソフトは提供しますから、そちらで合わせてください」というところが多かったため、ソフトの優秀さもさることながら、当社に合ったカスタマイズをしていただけるという提案は魅力的でしたね。
「バラ積み時代」を下回る運賃単価を実現
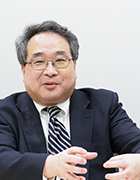
最上 氏
ー あらためて、取り組みの成果を教えてください
今回プロジェクトを実施したのは、当社の主力製造拠点の一つである東北製造所(敷地総面積22.3万坪)です。この拠点からの東北→四国ルートの運賃単価は、パレット輸送に切り替えた2015年4月以降、バラ積みをしていた2013年、2014年の平均単価に比べて14%の上昇を余儀なくされました。それが、2016年10月に新システムの運用を開始してから目に見えて下落に転じ、2017年(1~8月)の平均では、運用前に比べ17%のコストダウンを実現。単価自体の見直しも行ったのですが、再び積載率が上がり、「無駄なトラック」を削減できたことが大きく貢献しました。
そうした「目に見える成果」を得ることができたのも、現場の意識が変わったからですね。プロジェクトを始めた頃は、物流コストのアップも「相場が上がっているのだから、仕方がないだろう」という受け止め方でした。それが、取り組みが進むにつれ、「やればできるんだ」という意識に変わっていきました。そうした社員の意識改革も、確かな財産になったと感じています。輸送業者さんに「荷主がそこまでやってくれるのか」と感謝していただいたのも、我々としては大きな喜びです。
ー 技術的に一番ポイントになったのは、どこだとお考えですか?
トラックに、より隙間なく積み込もうとすると、「製品のサイズをミリ単位で計測して」という発想になりがちですが、そこはある程度割り切って、まずパレットに載せた状態の荷物の外形を「パレットサイズ」と定義し、それを10種類にパターン化しました。さらに、それらをトラックに積載する際の組み合わせ=「ポジション」を、全部で108パターンに類型化したのです。実際の積み付けでは、その中から最も効率のいいパターンを選択します。
こうして、効率的な積み付けプランを自動作成できるKKEの既存システムに、トラックへのバンニング技術などの機能を加味しカスタマイズした、当社独自の積み付け最適化システムを構築しました。
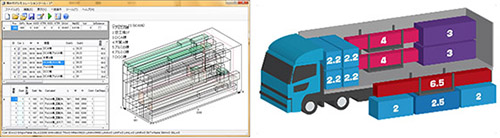
「幹線輸送」「2次配送」の再構築も視野に
ー 今後の課題についてお聞かせください
「工場を出た後」の物流も含めた効率化が課題です。いくらトラックの積載率が向上しても、行き先がバラバラな荷物が混載されていたら、意味がありません。積み付け計画と輸送・配送計画のバランスをどう取っていくのかが、ロジスティクスのトータルな効率化の大きなポイ ントになるわけです。荷物をデジタル管理できる当該システムは、この点でも可能性を開きました。すでに、工場から各地域までの「幹線輸送」、そこから工務店さまや施工現場への「2次配送」、それぞれの最適化に向けたプロジェクトを開始しています。
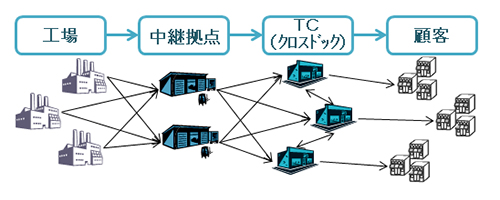
東北製造所のプロジェクトを進めつつ、今年度からは、他の製造拠点への積み付け最適化システムの導入を図っていきます。さらに目を先に向ければ、トラックの自動運転への対応、社内外との共同配送の検討といった、様々なテーマを見据えた運用が必要になるでしょう。当該システムの拡張性の高さが、そこでも威力を発揮してくれるのではないかと期待しています。
ー 最後に、当社に対するご要望がありましたらお聞かせください
東北の現場に足繁く通い、一つひとつ問題解決に当たっていただいたことに、大変感謝しています。今後も、我々の気付かないような点を、どんどん進言していただきたいですね。技術も人も、素晴らしいリソースをお持ちであることはわかりましたので、それをできうる限り当社の現場に振り向けて(笑)、一層スピード感を持ってサポートしていただけたら、というのが贅沢なお願いです。
取材日:2018年3月
YKK AP 株式会社について
創立:1957年7月
本社所在地:東京都千代田区
ホームページ:https://www.ykkap.co.jp/